Kevlar. The Mysterious Super Fiber.
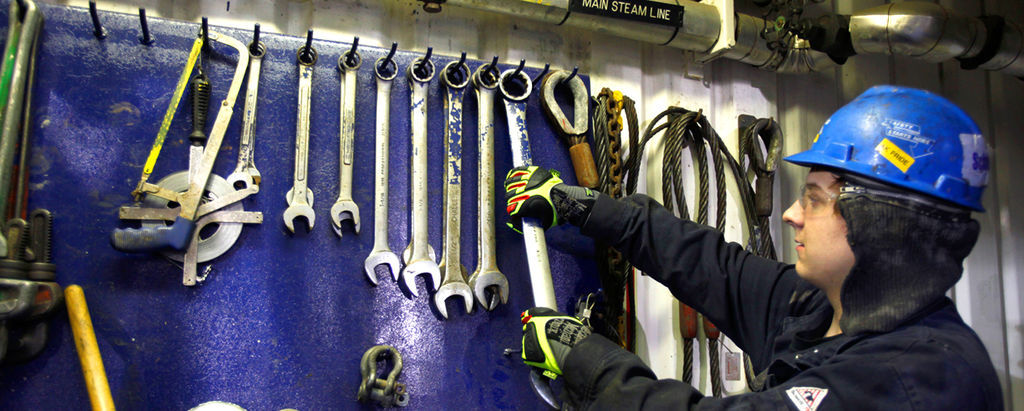
Poly-paraphenylene terephthalamide, or better know as Kevlar®, is the registered name given to this specially blended para-aramid synthetic fiber. While working for The Dupont™ Company in the 1960s , a Polish-American chemist named Stephanie Kwolek was given the task of developing a new lightweight fiber meant to replace the heavy and cumbersome steel cord used in car tires at the time. You see, even as early as 1964, the gasoline shortage of the 70’s was anticipated creating the need for more fuel-efficient cars. By combining a unique formulation of polymers, Kwolek discovered liquid crystals being formed in this “soup” of chemicals. At first the solution held little promise, but she was persistent and upon further testing discovered that after subjecting the solution to the “spinneret”, the fiber it produced did not break. This version of synthetics shifted polymer chemistry into an entirely new direction.. Beginning in 1971, Dupont introduced what we now know as Kevlar to the world.
Guess you can say Stephanie was the Mother of Invention. Nice.
Kevlar is really just an amazing version of plastic. Although, not plastic like a whiffle ball bat. Due to the unique chemical structure and long chain molecule arrangement, the ultra-tight knit fibers have characteristics that enable it, when woven into a material sheet, to stop a bullet and when braided into strands, to propel an arrow straight and true.
Exclusively owned and produced by Dupont, Kevlar is related to other fibers such as Nomex and the common Nylon, both also developed by Dupont. There are several blends of Kevlar constructed for specific and unique requirements. Kevlar 29 and Kevlar 49 represent two of the most widely used variations of the fiber. Common applications for Kevlar 49 fabrics include: kayaks, canoes, high-speed boats, aircraft panels, sporting equipment, and wind turbines. Kevlar 49 fabrics need to become a rigid, composite part in order to maximize their physical properties. This eliminates usage in a dry application such as clothing or soft body armor. Kevlar 29 fabrics are made of tough yarns that are built for ballistic protection. The ballistic level depends on several testing factors: type of weapon, caliber, bullet type, testing range, and projectile velocity. On many “soft shell” products such as gloves and knee pads, Kevlar 29 fabrics and fibers are suitable for panels and seam stitching construction.
Kevlar’s properties aid in distinguishing it from many other fibers and materials. Kevlar is strong but also very light. The tensile strength of the Kevlar fiber is over eight times stronger than of a steel wire. It also handles heat very well and can withstand temperatures well above 850ºF. Kevlar will burn but is easily extinguished by removing the heat source.. Kevlar is capable of remaining soft and pliable down to -320ºF. and is even slightly stronger at lower temperatures. Just like any super hero, Kevlar does have its weaknesses. Long exposure to ultraviolet light will cause discoloration and degradation in its fibers. Additionally, certain chemicals on the fibers can weaken it.
Kevlar is often combined with a variety of other materials to produce an array of composite materials. Popular marriages include Kevlar with carbon fiber and Kevlar with stretch materials like Lycra. The recognizable Yellow-ish color of Kevlar is its natural color. It cannot be bleached white but it is possible to colorize it in such shades as red or blue..
Mechanix Wear® is always on the lookout for better materials. Materials like Kevlar, ARMORCORE™, MATERIAL4X®, CARBONX®, ARMORTEX combined with manufacturing and design advancements results in products that offer a level of safety, protection and performance never seen or felt before. Strong, lightweight and potentially a lifesaving feature, Kevlar is a must-have in our tool-box of materials. Thank you Mrs. Kwolek.