MATERIAL4X. Strength, Not Size.
For the average Joe, the term “pleather” has become slang for the faux versions of real leather that are made from a variety of bits and pieces. When the original version was designed, developed and coined Pleather® it was cooler than the Fonz’s jacket. Now the name, because of all the imitation imitations, not so much.
But what exactly is artificial leather, and why not just use the real deal? Before plastics were introduced into the material equation there was a material called American Leather Cloth. It was a hodge podge of Calico, scraps and small pieces of leathers, oils and pigments of color all dried and pressed and embossed to emulate a “leather like” finish. This leather cloth was cool for a while but was really just a burley version of a Papier-Mache’. Then the chemists got involved. As all versions of imitation leather are a combination of man-made compounds and materials it only makes sense that companies like DuPont, Toray and Michelin design, develop and then produce these modern marvels of faux leather. There are many different versions of “leather like” materials, Corfam®, Koskin®, Leatherette®, Lorica®, Kydex® and Rexine® just to name a few. Naugahyde® is another brand of imitation leather which was first trademarked in 1936. It gained popularity in the 60’s and 70’s and remains one of the most widely used synthetic leathers even today. The common theme of the leather like materials is that they start with a fabric base, Polyester most often, and then top it off with a cocktail of polyurethanes to give it the look of various types of leather.
Cows and pigs weren’t the only ones pushing for a better alternative to natural leather. Fact is, we all know leather is awesome. It breathes, becomes softer and more pliable over time, can be many times stronger and resistant to tears or punctures and, for the most part, is hypoallergenic. But a natural hide has its limitations. It is not always a uniform thickness, it can have holes and imperfections and the yield of the hide is limited to the size of the animal.
The “Synthetic Leather” game took a giant step forward when a handful of Japanese Toray researchers were given a second chance to finish work on what they had been working on the previous few years. The fact that they were working on something that would be marketed as synthetic leather was overshadowed by what was found along the way. The fibers they developed to be used in the construction of the material is the magic. Stage entrance: An ultra-thin micro fiber. These fibers would allow the finished material to have a soft hand and feel luxurious and expensive, much like fine natural leather. Ultra suede was born. And was granted something like 250 worldwide patents. Nice. So that’s it? Not so fast. In the late 60’s, the Kuraray Rayon Company introduced its version of synthetic leather. Clarino was similar to Ultra suede but had several notable differences. Ultra suede is 60% polyester while Clarino is 60% Nylon. The construction of the micro fibers included in the finished material is different between the two as well. What sets Clarino apart is the process the material goes through to become the material. The initial chemical materials are created, spun, cut, interchanged together, needle punched, cleanser impregnated, coagulated, fiber extracted and then finished with a buffing. The finished Clarino bears more of a resemblance to natural leather in its structure and finish than many of its competitors.
In 1991 Mechanix Wear designed The Original® glove and used Clarino’s flagship material of the time, NASH 8080 in the design. The material was used on the palm and finger gussets and resisted wear, punctures and was highly resistant to abrasion. But most of all it was machine washable. Unlike the natural leather gloves found in the market, Clarino did not shrink, harden or retain moisture. For many years the primary users of The Original glove were auto mechanics. And the test bed for new glove ideas were the professional pit stop mechanics of the NASCAR racing world. Some guys wanted better feel, some guys wanted more heat protection. By using Clarino’s NASH in the construction of the glove the options of a thicker or thinner or special material coating or finishing applied to the material allowed the Mechanix Wear to develop gloves that addressed their specific needs.
Say Hello to "Hoss"
In 1995, Keith “Hoss” Armstrong started working for Newman-Hass Racing on the Indy car program and started to use gloves made with a synthetic palm. Love at first sight. In 1998, Hoss hooked up with Brian Lunniss from the Mechanix Wear R&D department and was introduced to the new M-Pact® glove. The glove used Clarino NASH 8080. He was able to get 2 full weeks from a set of gloves. Not much time you say? How about twice as long as the gloves he had been using. Dealing with hot tires, brake dust, corrosive chemicals, metals and aggressive grip tape wrapped around everything, Brian and Hoss thought they had something pretty stout. But if twice the glove life was good, then lasting 4 times longer would surely be better. So, the search and research began. Not being chemists could have been a problem. But Brian and Hoss knew what they wanted and what they needed and Mechanix Wear knew someone who could help.
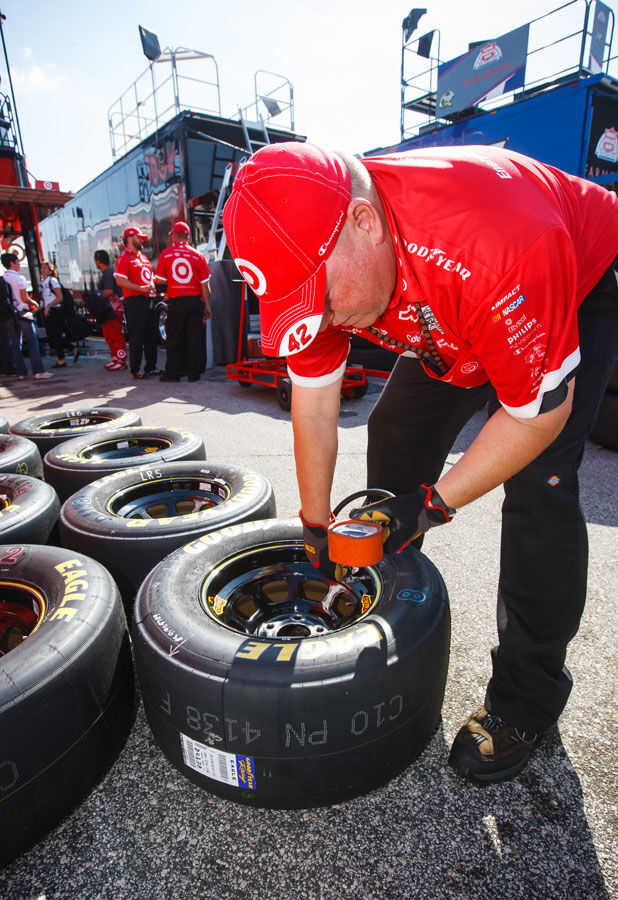
When the rubber meets the road. Thanks to guys like Keith, racing pushed the development of Material4X®.
Material4X®
The need: a material that included all the great attributes of NASH but was stronger and more abrasion resistant and tear resistant, without being too thick or too dense. The science was there. And so, started the material development. The first was too thick and soft. The next was too thin and slick and then viola, just right. After nearly 3 NASCAR racing seasons of actual in-use pit stop and shop testing, Material4X was ready to be introduced to the market. We think Material4X is pretty good stuff. So do ANSI and CE testing labs. How about Material4X testing out at 3,1,4,2 for abrasion, cut, tear and puncture while the standard is 2,1,1,1. Without giving up the material recipe for all to see, let’s just say it all adds up. Material4X is, as the name implies, 4 times the material the others say they have. Breathable, always soft and flexible in any temperature, highly abrasion resistant, high tear and tensile strength and as with all Mechanix gloves, machine washable.
(And the cows, pigs and goats all over the world sighed with a bit of relief)